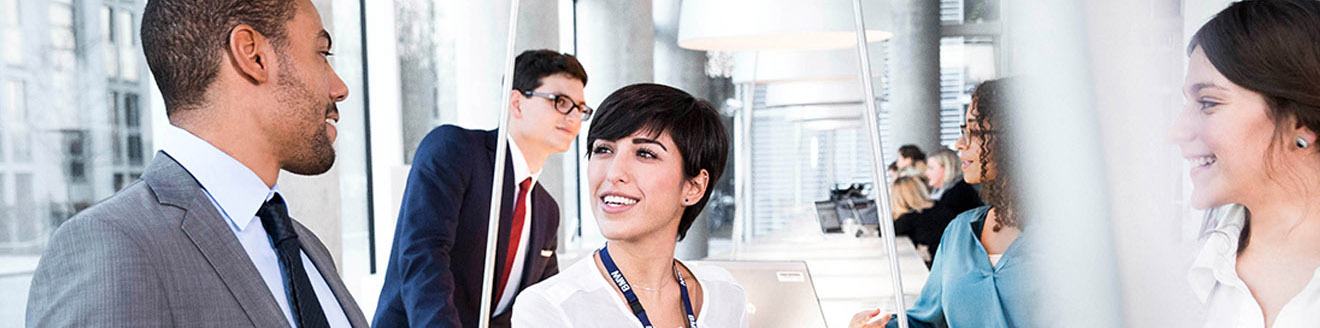
This review was submitted over 4 years ago, so some of the information it contains may no longer be relevant.
Rating
-
The Role
-
The Company
-
The Culture
- 1. To what extent did you enjoy your work placement or internship?
- 2. To what extent did you feel valued by your colleagues?
- 3. To what extent were you given support and guidance by management/your supervisor(s)?
- 4. How busy were you on a daily basis?
- 5. How much responsibility were you given during your placement?
- 6. To what extent did/will the skills you developed, and training you received, assist you in your degree studies and beyond?
- 7. What was the general atmosphere in your office?
- 8. How well organised was the overall work placement or internship set up?
- 9. In terms of personal training and development, to what extent did the company or firm invest in you?
- 10. What were the perks on your work placement?
- 11. How appealing are future employment prospects within the organisation?
- 12. Was there a good social scene amongst any fellow placement students/colleagues?
- 13. What was the cost of living and socialising in the area you worked in?
- 14. What was the Nightlife like in the area you worked?
- 15. Were there many opportunities to get involved in activities outside of work?
The Role
The placement provided opportunities to travel to different BMW sites and tours from colleagues on sites to learn about the different processes that were used in the production of a finished vehicle. Day to day work could vary from regular material test to investigations on broken or defects within parts. This day to day work included many different investigative techniques which were enjoyable to learn has not been part of my university degree. The role had a real hands-on nature to it which was really enjoyable.
Within my team, I definitely felt valued as a member of the group. This included taking on responsibility for different tasks and equipment. I was consulted by production colleges on work I had done from time to time, and as a team, we were often consulted on various production issues and events.
Through various internal channels, there was lots of communication between different groups within BMW. My supervisor was positioned off-site for four days a week which made face to face meetings difficult and there was no formal development process in my department for my internship. There were lots of opportunities to research and study the standards and technical specifications of the processes and theory behind our day to day tasks. Opportunities to present my work and receive feedback were limited.
The amount of work varied from week to week as most of the work that I was a part of was submitted to our team from other staff. It ranged from having three or four tasks running concurrently to having a three-week gap without work being submitted to me where I work on internal tasks, such as researching test methods and equipment. These gaps in work happened multiple times throughout the placement. Tasks could range from a couple of hours to over a week at a time, these ranged from basic material checks which were the most common to longer failure or strain analysis tasks. I was also working on internal tasks from time to time such as working on IT setups within the lab environment or organisational tasks.
I was encouraged to take on responsibility locally within the team. I ran cleanliness checks in our facilities. I was also given the responsibility of some of the equipment; checking equipment histories, calibrations and work instructions. I produced a new work instruction for a large piece of equipment as part of this. I was not given responsibility on any projects beyond the tasks submitted.
The role required the ability to write technical reports which is something I developed during my time on placement as is a skill I will definitely employ on my return to university. As part of this, I have a much greater understanding of national/international testing standards and how to use them in my own work. I have built upon the limited materials education I had in my degree to develop a much greater understanding of material properties and testing.
The Company
Most days in the office were quiet, this was mainly due to the nature of the majority of the day to day jobs being individual tasks which meant collaboration across the three-person team was limited. Occasionally if a new request or sample was presented to the lab, we would gather and discuss it, but normally the office atmosphere was quiet and reserved.
The placement had been running for quite a few years when I joined, so there was a back catalogue of placement student work that had been done previously that I could read to get an understanding of the work they had produced during their time with the company. As a result, when applying for the role there was an accurate role description of the placement year on the careers website. Once I had sent off an online application, there was a long wait for a response which with some chasing lasted about two months. However, once a response to my application had been received, communication was often and thorough through the interviewing process up until the job start.
The training in the role was all done by the outgoing placement student who had a one month long handover period with me which involved a lot of hands-on learning of various testing methods and how to use the equipment. This was all done person to person and was fairly informal alongside some company wide training procedures either done through video or Skype. A lot of the learning and development was self-taught with occasional feedback on my reports.
Subsidised Canteen
National Travel
Above 25 days holiday
Future employment prospects within the team that I was a part of during placement is limited due to the small size of the team and the limited workload. Other opportunities exist within the organization due to the wide range of disciplines that BMW offers within the UK. There is a range of grad-level jobs that BMW/MINI/Rolls Royce offer on the UK. Within the production sector, most of the design and testing roles are located in Germany with smaller teams in the UK, so material and engineering-specific roles are limited within the UK.
The Culture
There were only two placement students on the Swindon site. There was no social scene locally amongst the placement students and there seemed to be little in terms of company social activities that were organized during my placement. However, on the Cowley site, there seemed to be a much healthier social scene amongst apprentices/placement students that was encouraged by the company.
The cost of living in Swindon was low, and housing was fairly easy to come by in preparation for moving to the area. The canteen on site was very good value and offered a good selection throughout the week. Bars and restaurants in the area are cheap and there are lots of sports clubs in Swindon that I was part of during my placement period.
The nightlife was limited, due to a low young population in the area as there was no university or similar in the area. Most of the nightlife that I was a part of was through the sports clubs I was part of during my placement, which was cheap and cheerful.
I was part of a range of sports clubs within the area, which was very fun to be a part of outside of work during my placement year. BMW did have a few charity events throughout the year, however they seemed to be more focused on Cowley over Swindon for the big events.
Details
Placement (10 Months+)
Automotive Engineering, Manufacturing, Material & Mineral Engineering
South West
July 2019